Checking Complete Closure of Tools with Inductive Proximity Sensors
Presses used to mold automobile body segments are fit out with rams. These rams hold an upper tool half in position as they press down on the lower half.
The process of changing tools occurs automatically. It means that before the ram loses the top half for tool change, the tool pair must be in the closed position. So tool halves are completely aligned when the automatic tool-change process initiates. This prevents harm to both tools and presses.
But how?
The inductive sensors can be the solution
How do these sensors work?
A single sensor is boarded on the lower tool housing. Before releasing the tool, this sensor is sampled. The target does not enter the switching range until the tool is completely closed. This prevents too early separation of the tool.
The accuracy in switching distance of these sensors is achieved if the upper half is only separated when the tool is completely closed. This happens with enough speed and consistency.

Advantages:
• Reduction in downtime
• Reduction in harm to both press and tools
To know more about inductive sensors and other kinds of proximity sensors, check out types of proximity sensors.
Want to know more about these sensors? Check out our article to learn about Inductive Sensor.
Among the leading manufacturers of automotive sensors, Contrinex is one of the largest. Step in to get to know Contrinex company.
Do You Need Help For Field Installation?
We have thought everything through, submit your request for an on-site support.
Do You Need More Solutions? Have a Look at Our Vast Applications
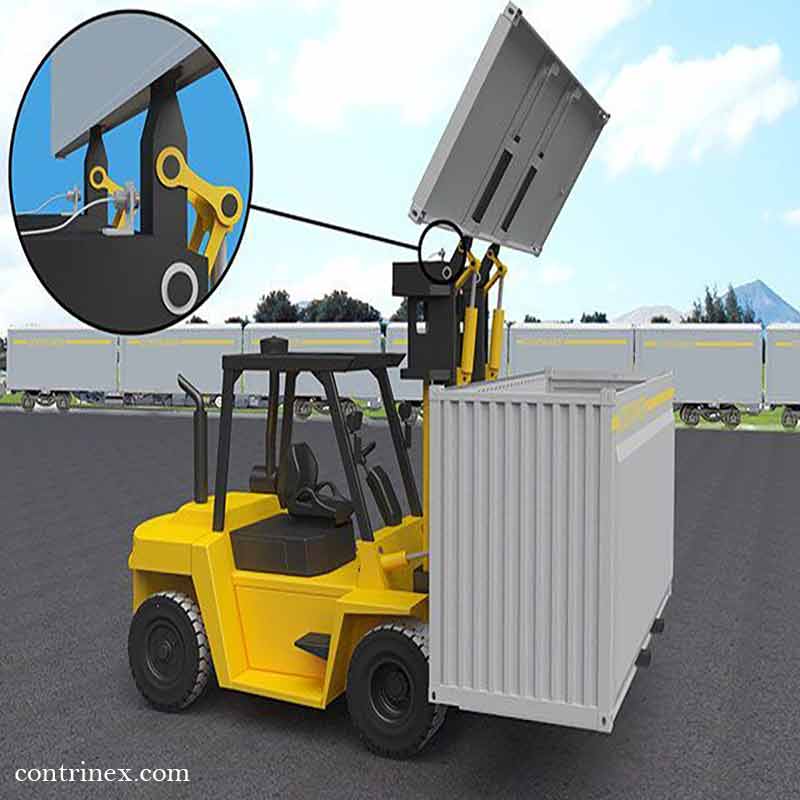
Position Detection of Forklift Forks When Opening Container Lid by Rugged Inductive Sensors
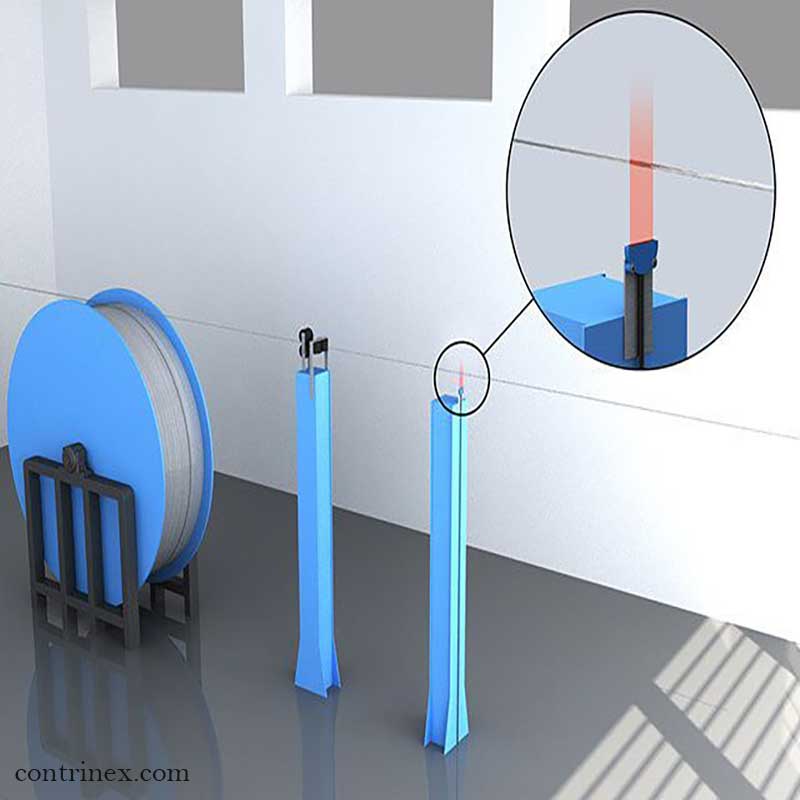
Identification of Faulty Units during Production of Parking Cables
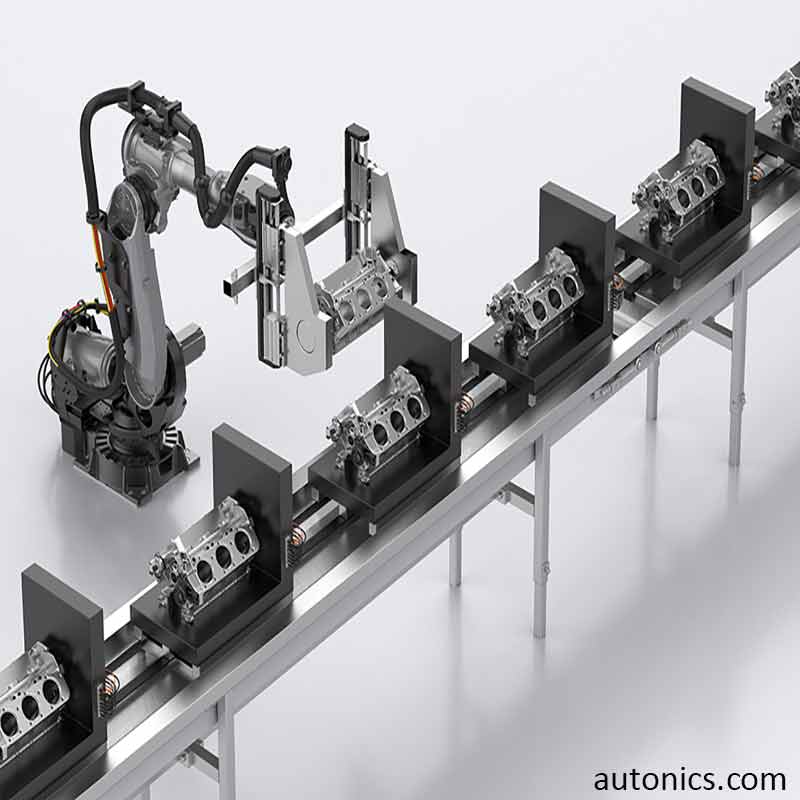
Manufacturing Automobile Components
Related Products