Checking the Engine Part Position during Manufacturing with Inductive Sensors
By the cylinder heads' arrival at the transfer station, the workpiece carrier holding them should stop. This stoppage takes place when sensors on the roller conveyor detect the arrival and make the conveyor stop.
Automatic position checking is demanded for the conveyor's stop and restart.
For this challenge, extreme range inductive sensors are the solution:
Compact inductive proximity sensors ensure the safe, reliable implementation of this task.
Set-up and function:
The sensors are set up on the conveyor. When an incoming workpiece carrier reaches the second sensor, it is in the appropriate position. So, the roller conveyor stops, and the robot gets enabled.
After removal of the cylinder head, the third sensor warrants the right onward path taken by the empty workpiece carrier.
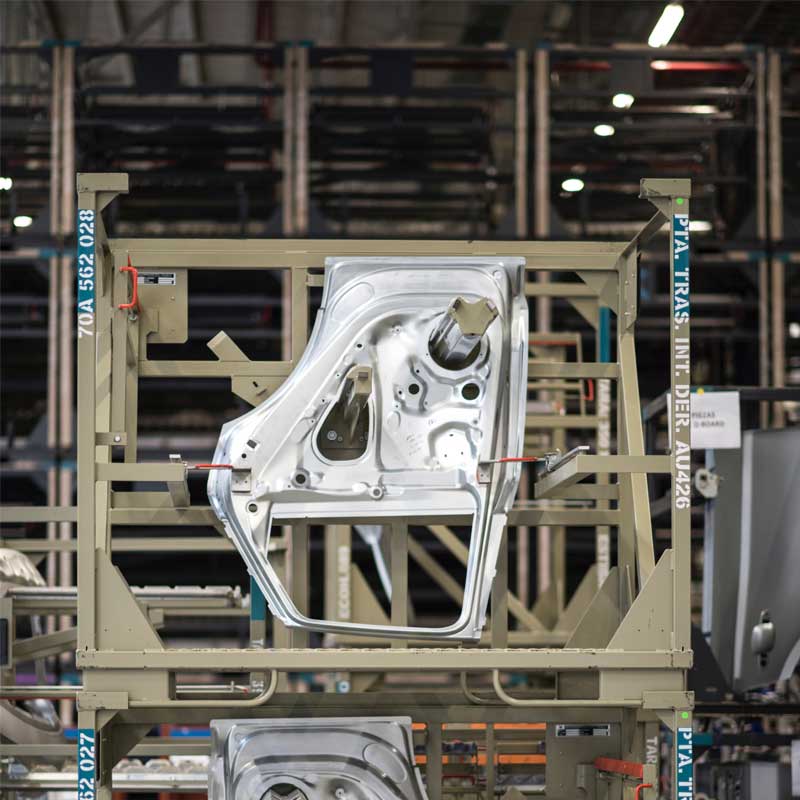
Advantages:
• High accuracy and reliability in the switching distance
• The stopping of the roller conveyor takes place at the right time
• The transfer process happens as safely as possible, with great speed and consistency
• Higher automated transfer stations' production speed
• Reduction in wastage, downtime, and equipment damage
you can get more familiar with this solution by clicking on the inductive proximity sensors.
But there is still one question left: do you want to know how these sensors work? If so, check out our article on proximity sensor working principles.
Among the leading manufacturers of factory automotive sensors, Contrinex is one of the largest. Step in to get to know Contrinex company.
Do You Need Help For Field Installation?
We have thought everything through, submit your request for an on-site support.
Do You Need More Solutions? Have a Look at Our Vast Applications
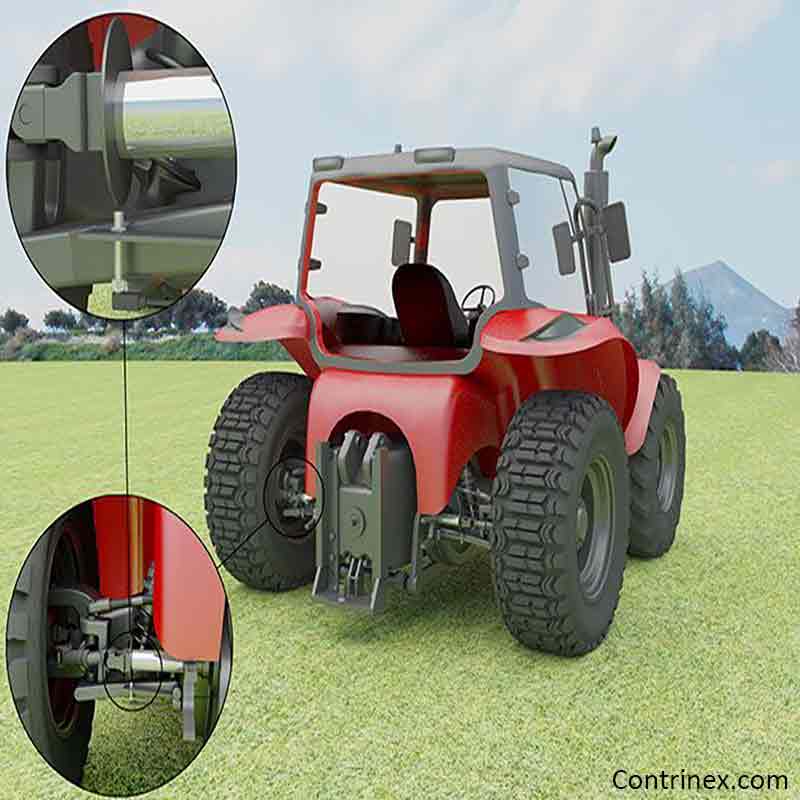
Detecting Straight-Ahead Status of Rear-Wheel Steering by Rugged Inductive Sensors
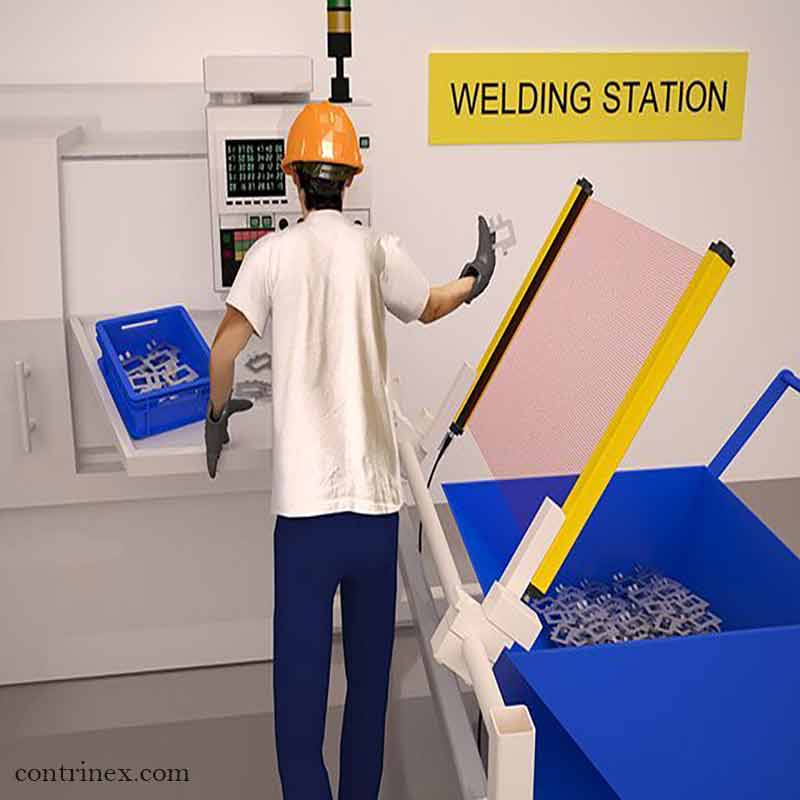
Identification of Incomplete Units by Infrared Light Curtains
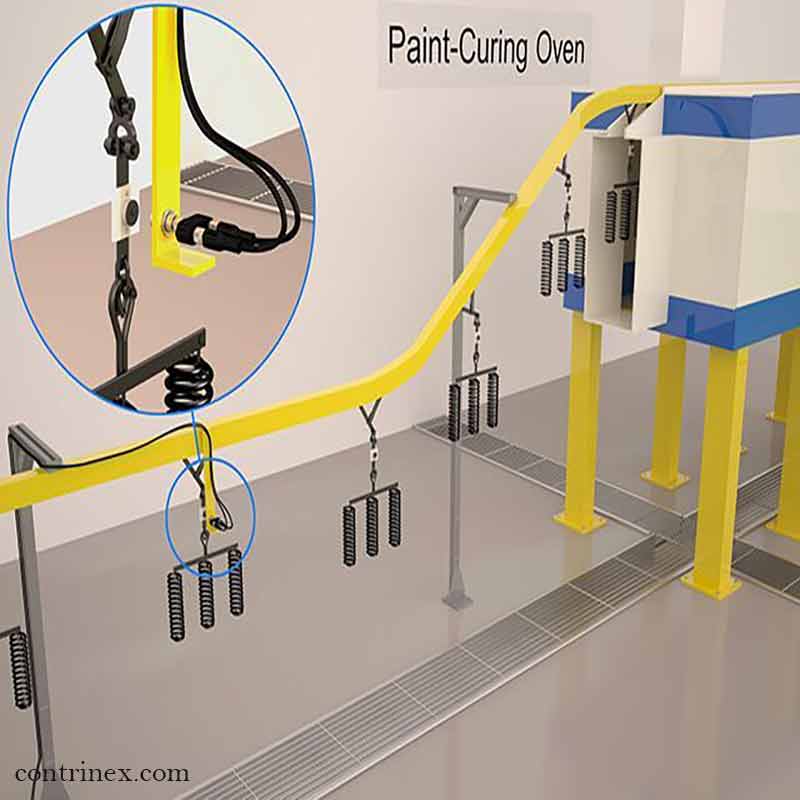
Heat-Proof RFID Tags for Automotive Painting Process
Relared Products