Food-Grade Inductive Sensors and Their Resistance to the High-Pressure Washdown Cleansing Process
Cleanliness is too essential in food-processing facilities. Clean-in-place (CIP) and high-pressure washdown systems are used in these facilities. So, manufacturing equipment (including sensors) for washdown areas should resist harsh cleansing chemicals. They also must be able to tolerate high-pressure water jets.
What type of sensors can help us?
Food-grade inductive sensors are designed for this application.
Features of these sensors:
• Corrosion-resistant
• Pressure-resistant (up to 80 bar)
• IP68/IP69K rated
• Highly robust
• A selection of one-piece M12-, M18- or M30-diameter AISI 316L /V4A stainless steel bodies and sensing faces or M12-diameter AISI 316L/V4A stainless-steel body
• PPS (polyphenylene sulfide) FDA-approved sensing face
• Suitable for most demanding environments
• Industry-standard PNP or NPN outputs with an integral M12 connector and IP69K-rated cable set
• Compatible with the current systems of the factory
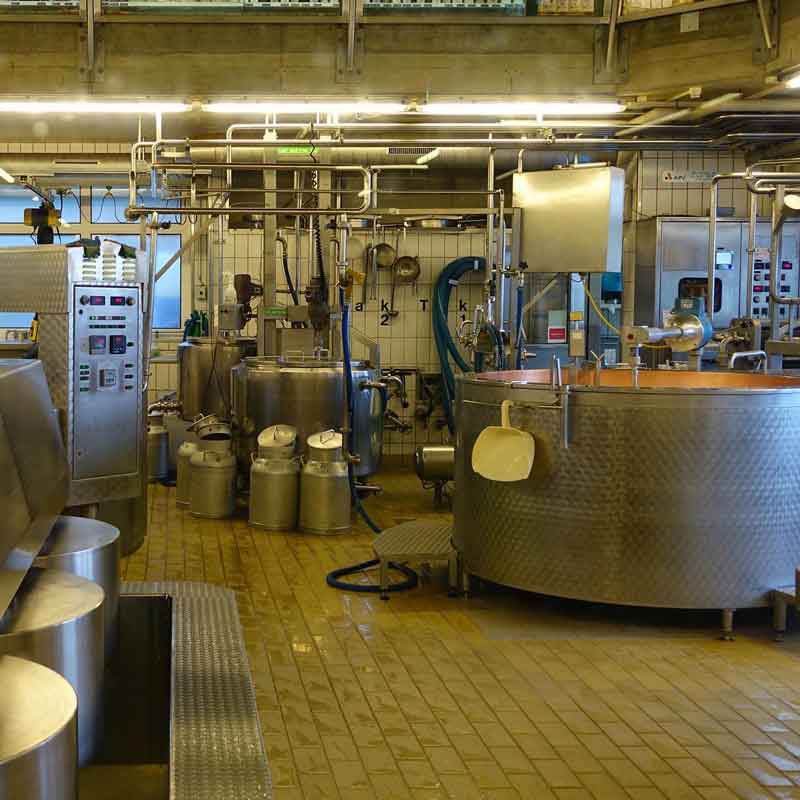
Other applications of Washdown sensors:
1. Flow control during milk-product processing
2. Position sensing of rotary-valve actuators.
3. Presence detecting: Various M30-diameter devices located on panels detect the presence of a locating feature. So, they admit that the proper ports are interconnected before CIP cleansing starts.
4. Positional control: Washdown inductive sensors sense the status of a cam on the shaft in making soft cheese from curd. So they admit the degree of angular circulation at preset intervals. These M18-diameter one-piece stainless-steel devices with optimal detecting distances are entirely suitable for the application.
5. Filling and packaging: The process in high-volume soft-cheese manufacturing relies on status detecting. Failure to synchronize cylinder extension with conveyor movement causes harm both to products and the equipment. Two washdown sensors embedded in the wall of cylinders detect the ram's presence as it attains the limits of its travel in each direction.
6. Sensors with IO-Link interface: Factory-wide communication is one of the demands of manufacturers.
Availability of IOLink for all sensors incorporating its patented ASIC technology has been announced. IO-Link is enabled on all normally open PNPs at no additional cost. It provides the benefit of digital communication in washdown areas without special cabling. In dairy-food production, processes run with remote diagnostics requiring almost no manual intervention. IOLink polling allows system integrators to determine remotely that the correct sensor is in the right location. IO-Link washdown sensors also feature an on-demand self-test that always admits fault-free operation.
Lastly, the sensor offers an output-position check derived from its plant calibration data. An alarm will be sound if the sensor output signal is out of range corresponding to the 80% to 100% nominal detection distance.
7. Food industry
There is a lot more to know about these sensors. Check out our article on proximity sensor working principles.
Also if you are curious to view the category of these products, click on inductive proximity sensors.
Among the leading manufacturers of factory automation sensors, Contrinex is one of the largest. Step in to get to know Contrinex company.
Do You Need Help For Field Installation?
We have thought everything through, submit your request for an on-site support.
Do You Need More Solutions? Have a Look at Our Vast Applications
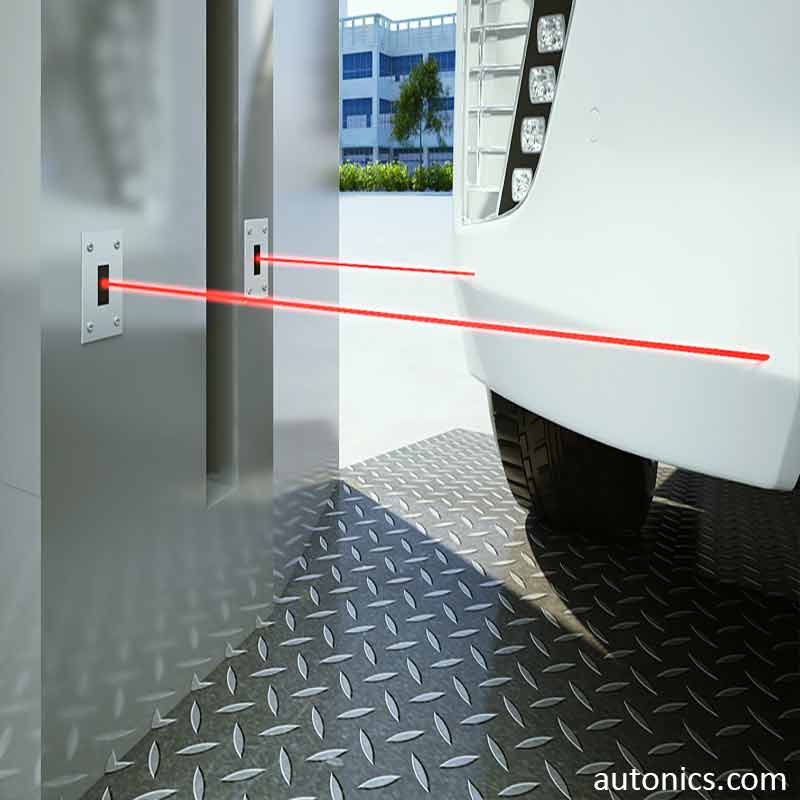
entry/exit of parking towers
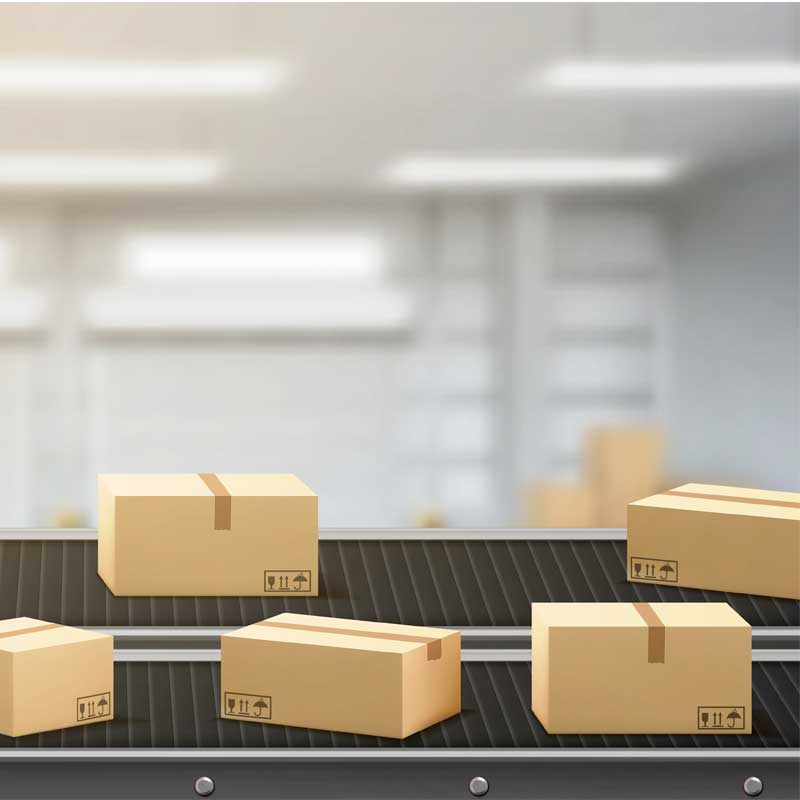
Figuring Out the Status of Cartons in the Packaging Process by Miniature Photoelectric Sensors
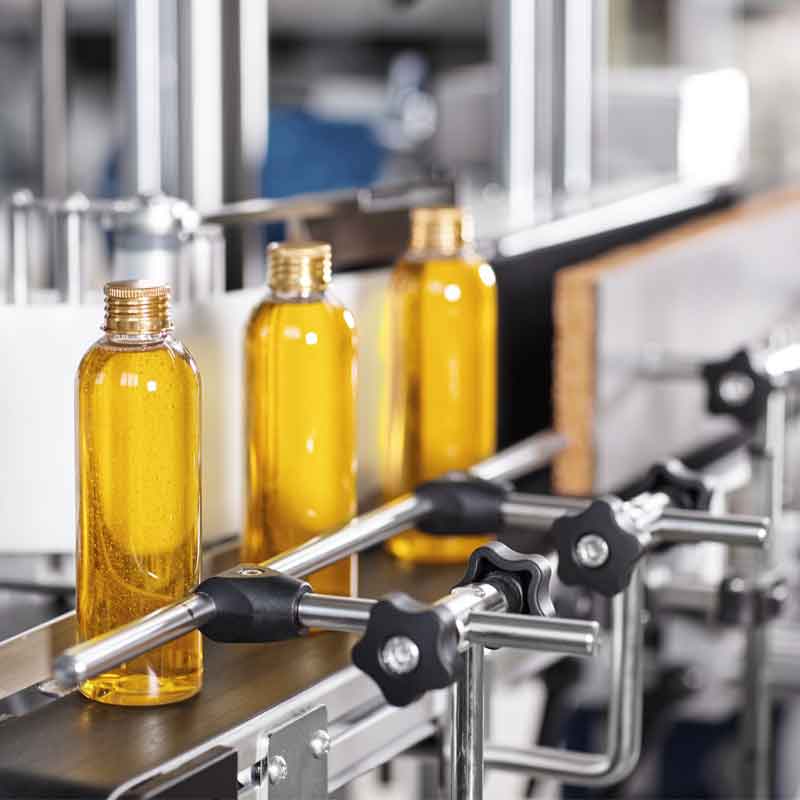
Capacitive Sensors Applicable In Quality Check to Ensure Presence of Bottles Caps
Related product