Minimizing the Cost of Quality through In-Process Position Sensing
Without a real-time estimation of the location of the reinforcement during manufacturing of industrial timing belts, we can just test product quality at intervals via cutting samples of extruded belts and taking optical measurements. This process is gradual and merely figures out errors after the manufacturing is complete, resulting in excessive reject costs. The customer requires specific sensors with analog outputs to estimate the location of steel reinforcing bands.
M18-size inductive sensors are suitable for this application. Patented Condist® technology offers a surprisingly stable sensing performance at working distances ≤10 mm with exceptional detection accuracy, incredible repeatability and resolution in the micron range.
The sensors use sample at 250 Hz, best for estimating the location of the steel reinforcement in the rapid moving belt profile, and supply continuous, non-linearized 0-10 V analog output signals. They are proof against vibration and alterations in ambient temperature, permitting positioning instantly after the extrusion press in close proximity to the moving belt.
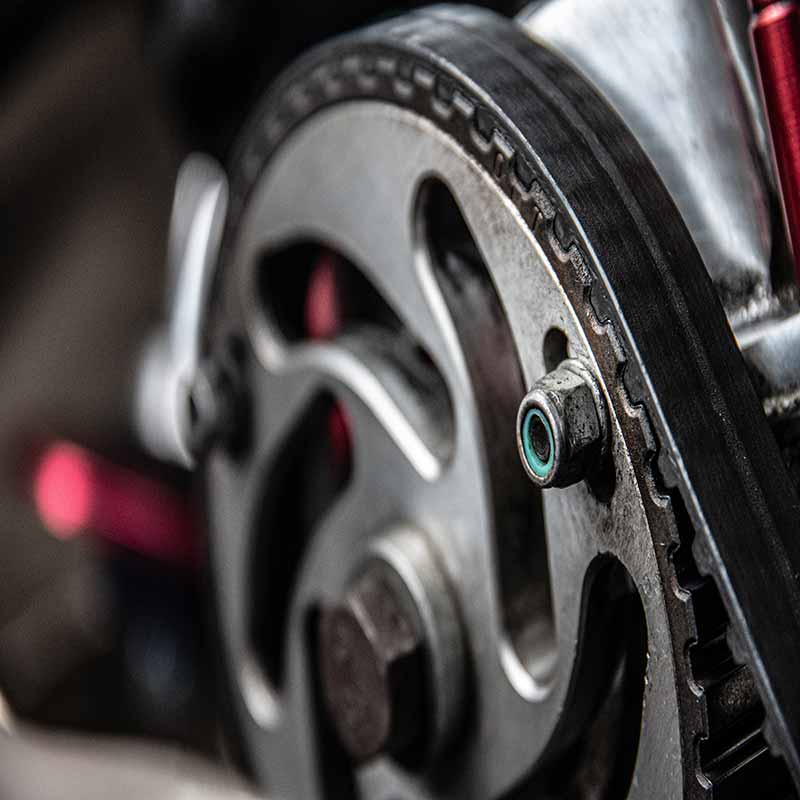
The gently tensioned belt clears the sensing face of the instruments by a few tenths of a millimeter. Connection to the customers' control system is provided thru a cable with an S12 connector.
Inductive sensors are small enough, high-accurate, reliable and affordable.
Do You Need Help For Field Installation?
We have thought everything through, submit your request for an on-site support.
Do You Need More Solutions? Have a Look at Our Vast Applications

Keeping Conditions under Control in Automated Assembly via Inductive Sensors

Minimizing Expenses and Saving Space in Contactless Hand-Sanitization Equipment Using Compact Dual-Mode Photoelectric Sensors

RFID Tags: Appropriate Devices for Precise Detection of Position of Rail-Mounted Conveying Machines
Related Products