Networked Beer Tanks: Applicable for the Breweries as Well as the Landlords
Large pubs have two beer tanks. Previously, the inspection of these tanks was the responsibility of the operators. Therefore, sometimes it is either not done accurately or it was not done at all. The new smart M2M (machine-to-machine) solves some of these problems. For this automatic exchange of information between the measuring devices in the warehouse and the brewery, the mobile network and the Internet are used. Among M2M's other benefits, we can mention that it warrants that landlords have adequate fresh beer at all times. Special pressure sensors use pressure to measure the temperature of beer tanks and their filling level. In the past, data was recorded using a data logger-live data was not available. But today, thanks to the Internet and the M2M solution, live data is being synchronized. In fact, with the help of M2M technology, the program detects that the tank beer is running out and consequently sends a new order.
Synchronized data allows you to save money and the environment
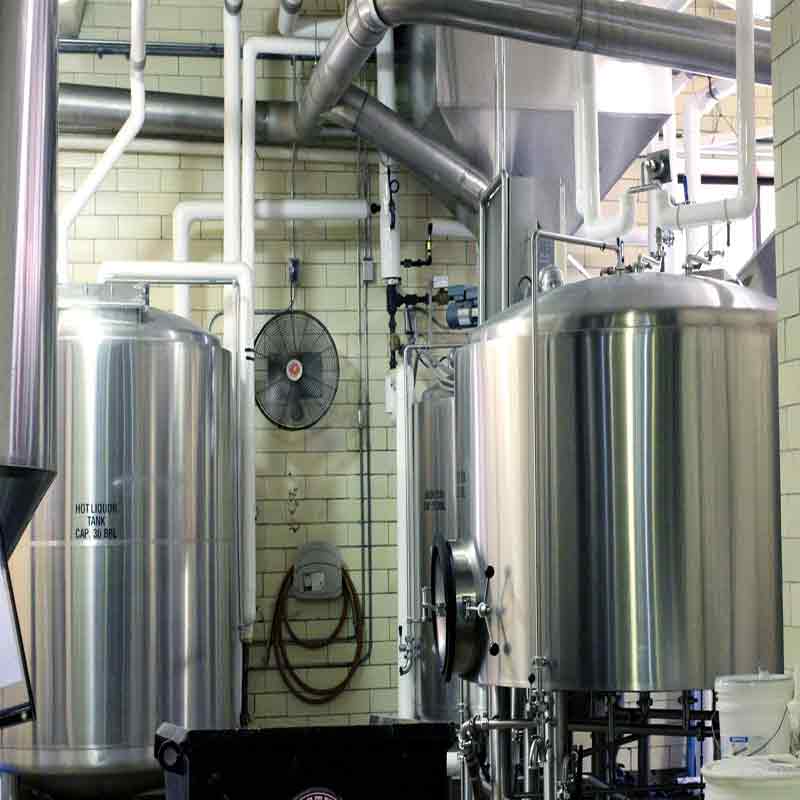
In addition to the above, M2M technology prevents transportation that previously seemed necessary, which in addition to protecting the environment, reduces additional costs.
In addition, the cost of data transfer is less than the operators' wages.
Permanent data transmission from tanks to myBeer app
A mobile phone company in Switzerland has developed an application called myBeer.
The tank content material is calculated on the inside with two pressure sensors fitted. One of these sensors is positioned at the top of the tank on the compressor inlet and the second is at the outlet at the bottom, in front of the riser check valve. The tank content is measured according to the pressure difference between these sensors, the traits of the beer and the size of the tank.
A box with integrated mobile communications module records the calculated values from the sensors at intervals and sends them through GPRS to a FTP cloud server along with additional information. The data is then interpreted, processed and accepted via the myBeer app.
The module and sensors are energy ed through a mains adapter. An accumulator is likewise included as a back-up measure to assure supply for a number of days to weeks if needed. If this occurs, promptly the system will then send a warning signal.
Tank temperature is likewise important, because it determines the flavor and shelf life of the beer. As such, temperature data may be utilized as an effective quality indicator.
Do You Need Help For Field Installation?
We have thought everything through, submit your request for an on-site support.
Do You Need More Solutions? Have a Look at Our Vast Applications
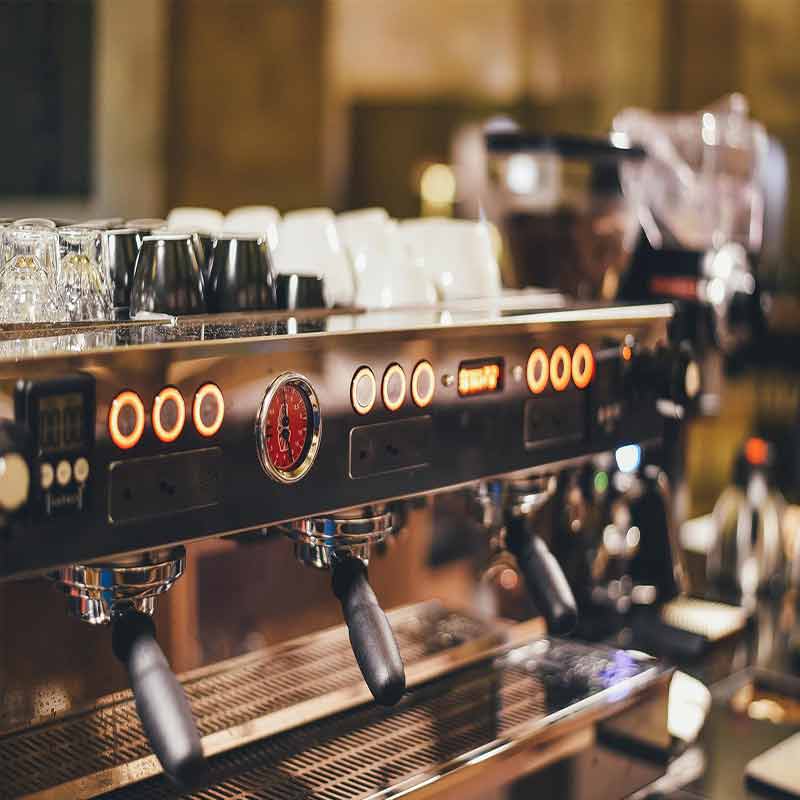
Pressure Sensors for Regulating Pressure in Coffee Machines
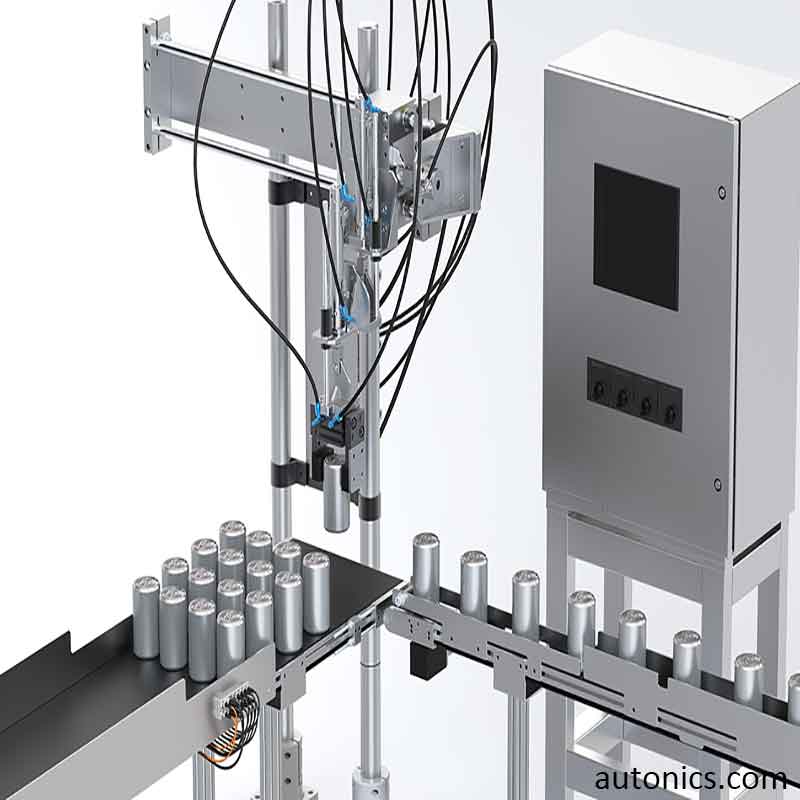
Selected Applications From Food and Beverage Industry
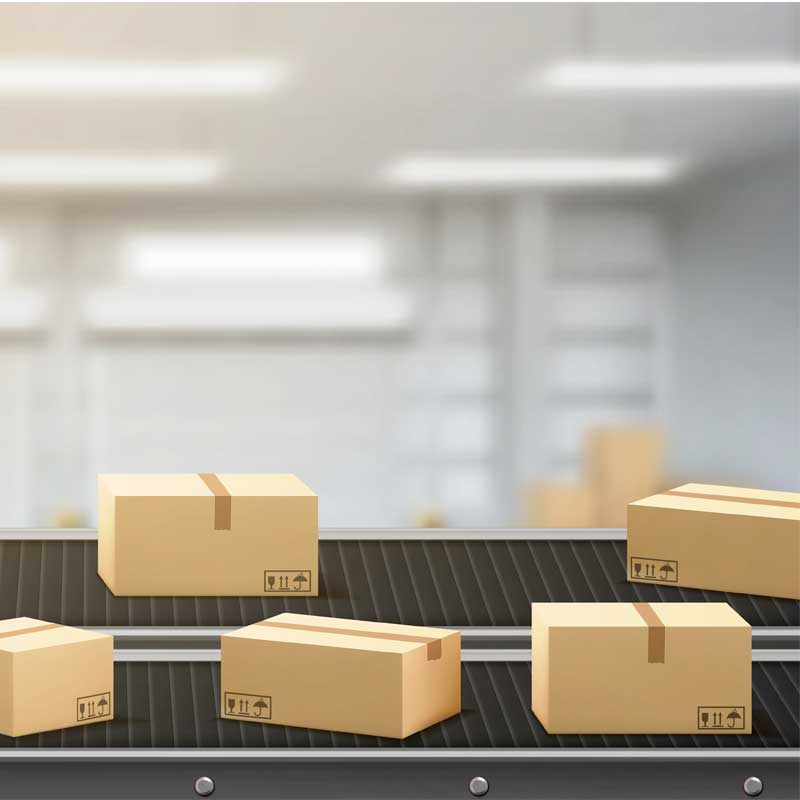
Miniature Photoelectric Sensors for Figuring Out the Status of Cartons during Packaging
Related Products