Protecting Components against Collision in Automated Manufacturing via Embedded Miniature Photoelectric Distance Sensors
Throughout automated manufacturing of electronic equipment, compact multi-finger robot grippers convey elements among operations. If a malfunction or an unplanned human intervention occurs, there will be an unacceptable collision risk. While anti-collision measures will generally be coded into software routines, this is not usually enough. Engineers insist on an overriding anti-collision system.
Grippers equipped with photoelectric sensors are a dependable and affordable way of estimating the proximity of obstructions in real time. While transporting elements among operations, these miniature distance sensors, embedded in the outward-facing surfaces of the gripper jaws, detect the status of potential obstructions throughout travel.
These miniature tools weigh just 3.1 grams, and with a compact 4mm x 4mm x 11m envelope and no outside housing, they provide easy integration in tight areas with inadequate room for conventional tools.

These sensors have sensing distances of as much as 40mm. An industry-standard PNP analog output guarantees ideal flexibility, with an output variety of 0.3V to 3V providing scope for in-situ adjustment. Connection is through a four-wire PVC-sheathed cable with a two-meter standard length.
Do You Need Help For Field Installation?
We have thought everything through, submit your request for an on-site support.
Do You Need More Solutions? Have a Look at Our Vast Applications

Protection of Fragile Electronic Assemblies against Harm through Automated Manufacturing via Embedded Miniature Photoelectric Distance Sensors

Checking Complete Closure of Tools with Inductive Proximity Sensors
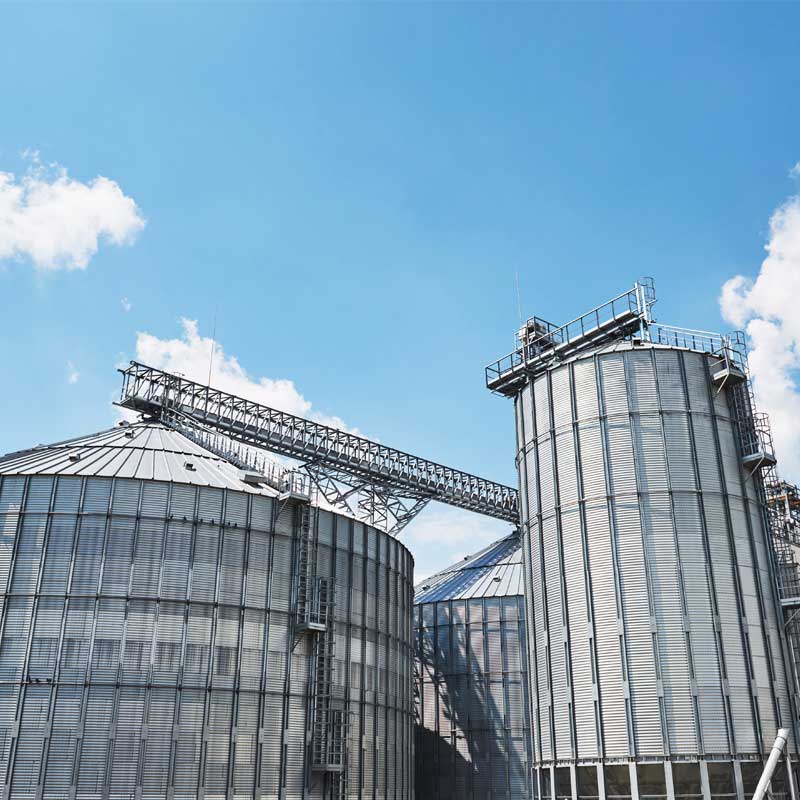
Making the Employees Safe In Process Of Degreasing Tanks by Using Safety Light Curtains
Related Products