Providing Significant Preservation with Minimum Cost in MF Resistance Welding of Aluminum Assemblies by Factor 1 Weld-Immune Sensors
The robust magnetic fields generated via industrial spot welders impose fail or break down to unprotected sensors. To avoid misalignment throughout assembly, we need inductive proximity sensors that resist the incredibly excessive currents required to weld aluminum components.
Weld-Immune inductive sensors are appropriate for this application. They detect aluminum targets throughout an automated MF resistance-welding process. It is a true Factor 1 sensor, detecting targets in steel and aluminum similarly efficiently with no decrease in detection distance.
An M8-diameter Weld-Immune sensor, positioned along the lower welding electrode, verifies that the frame is efficiently placed and activates the welding sequence.
The sensors' rugged construction comprises a metallic housing and a temperature-resistant sensing face in a high-strength PEEK polymer; the robust magnetic field does not impact on the sensor’s performance. The M8 sensor has a sensing distance of as much as two mm. As an actual Factor 1 sensor, there is no need for correction factor for the aluminum target.
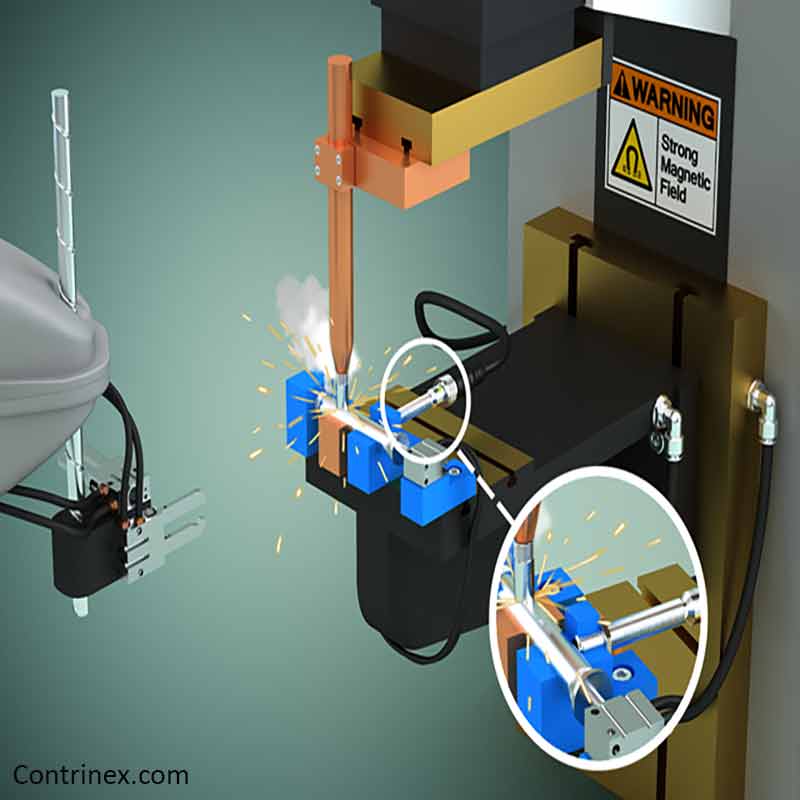
These sensors are available with an ACTIVSTONE® coating, a high-performance ceramic layer that is specifically immune to weld spatter. Outside surfaces of the sensor are protected, stopping spatter accumulation and optional spatter-resistant shrouding can cut off cable damage.
Do You Need Help For Field Installation?
We have thought everything through, submit your request for an on-site support.
Do You Need More Solutions? Have a Look at Our Vast Applications
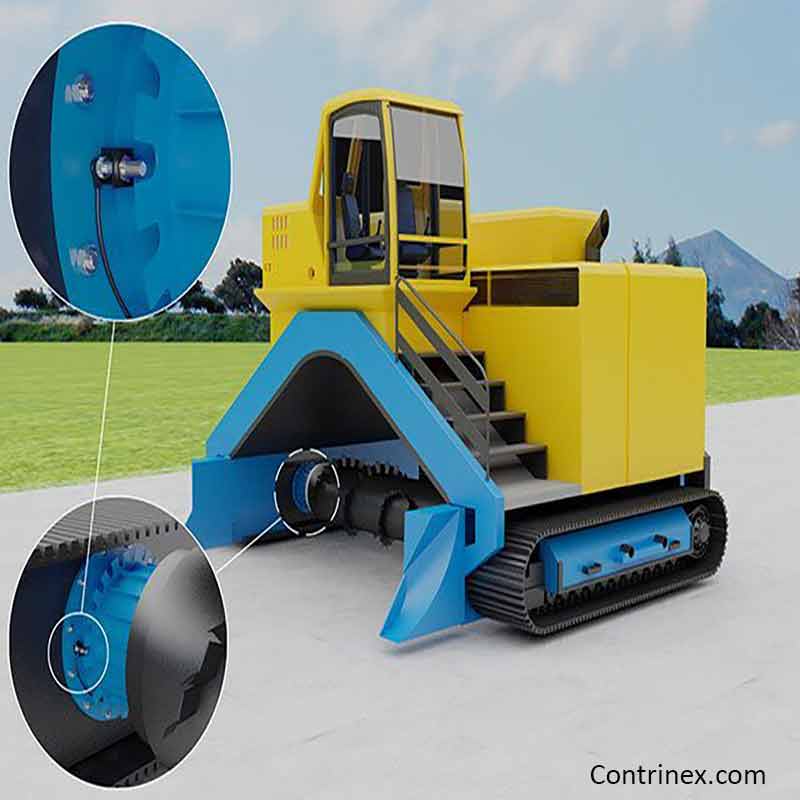
Checking the Speed for Mobile Compost Turning Equipment
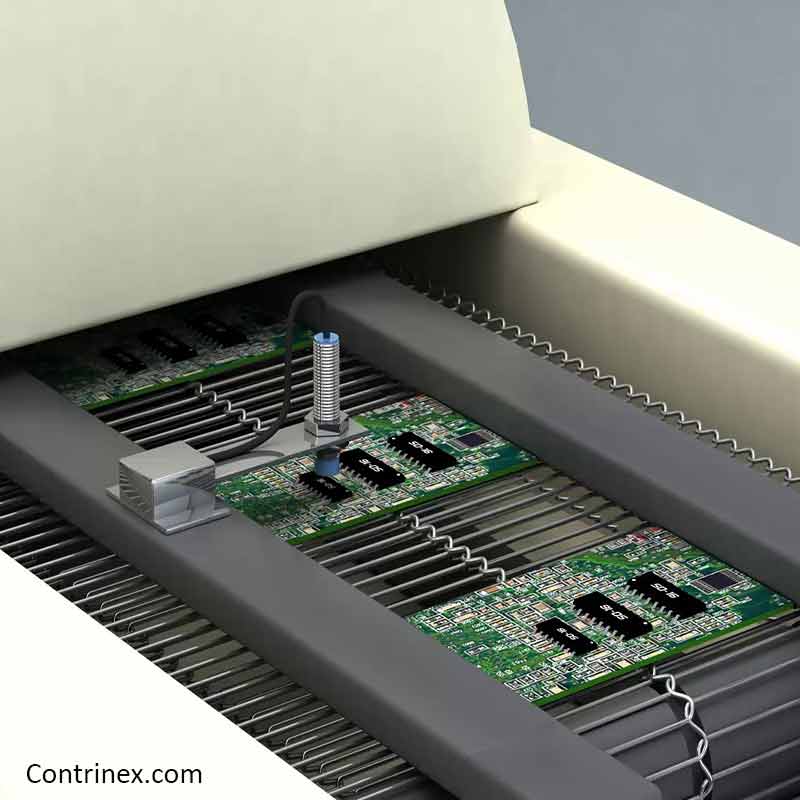
Controlling Reflow Soldering Process through Detecting Circuit Boards
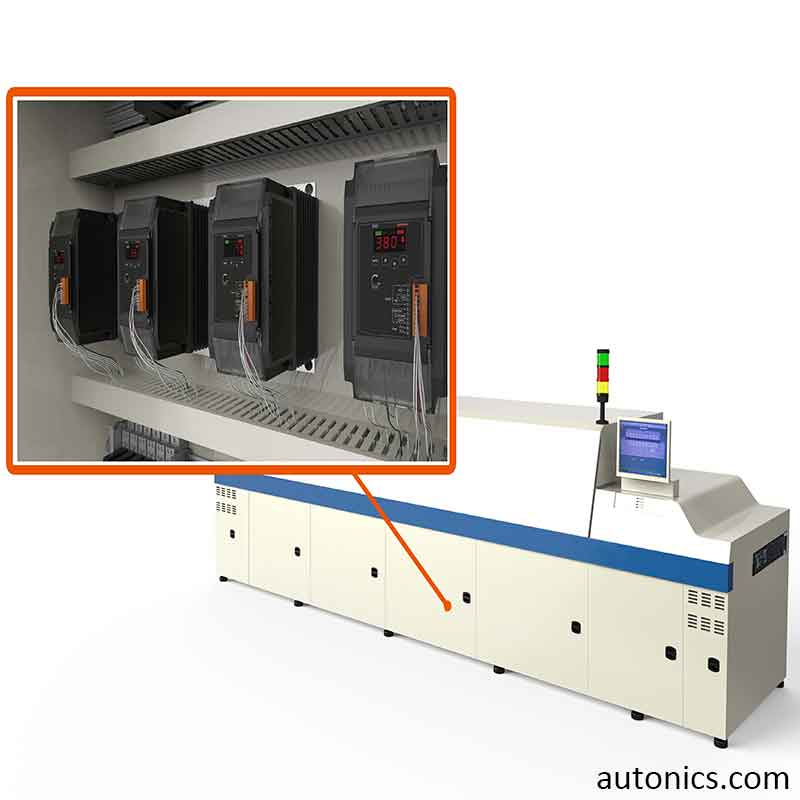
Selected Applications From Machine Tools Industry
Related Products