Warranting Thorough Closure of Tools Using Inductive Proximity Sensors
The process of changing devices in presses used to mold body parts of automobiles has been automated. These presses are supplied with rams. It is critical that before the ram releases the top half of the device for device changes, the device pair be in the closed status. This minimizes the harm to either press or tool and any resulting downtime.
Inductive sensors are suitable for this application, thanks to their vigorous industrial construction and the high reliability they have.
A single sensor is integrated into an external angle bracket on the lower tool housing. Before triggering tool release, this sensor is sampled. Because the target does not enter transition range until the tool is completely closed, premature tool release is avoided.
The precision of the switching distances of these sensors means that the top half of the tool is released just when the tool is perfectly and completely closed. This happens with all the consistency and velocity expected of an automated factory process.

Downtime and harm to press and tools are prevented by avoiding the press from proceeding to the tool-change process with imperfectly closed tools.
Do You Need Help For Field Installation?
We have thought everything through, submit your request for an on-site support.
Do You Need More Solutions? Have a Look at Our Vast Applications

Safety Light Curtains for Keeping Operators' Fingers Safe on Hydraulic Presses
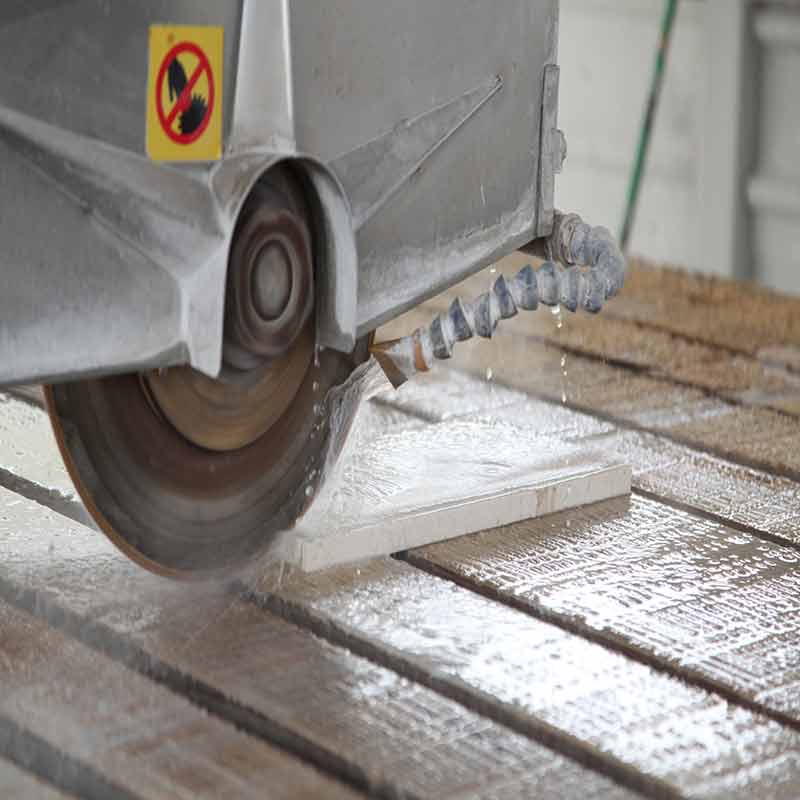
Supplying Stroke Feedback in Pressure Intensifier of Water Jet Cutting Machines via Inductive Sensors
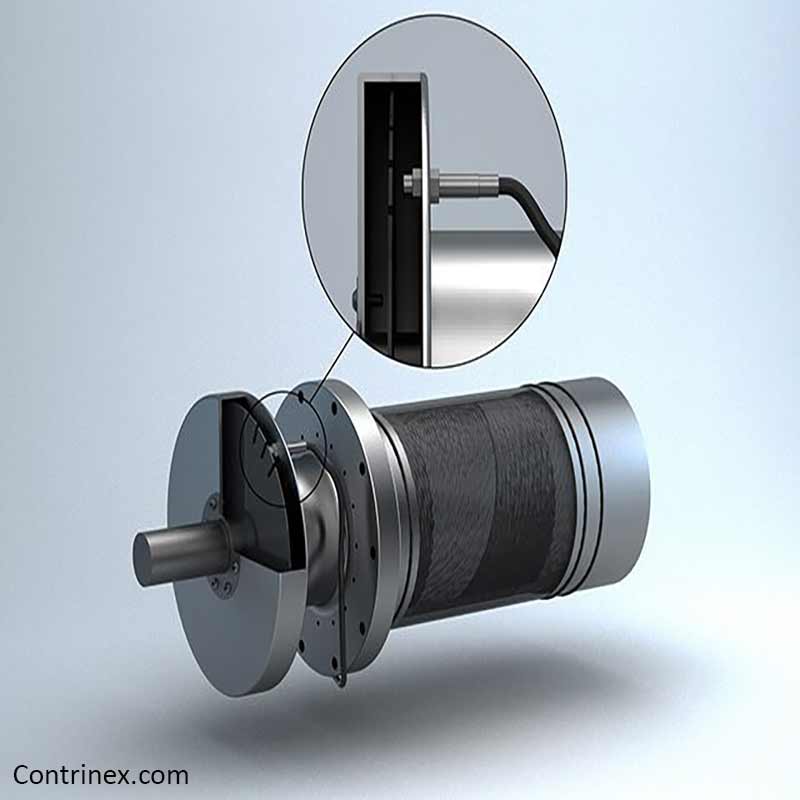
Precisely Figuring Out High-Speed Spindles' Direction Using Miniature Inductive Sensors
Related Products